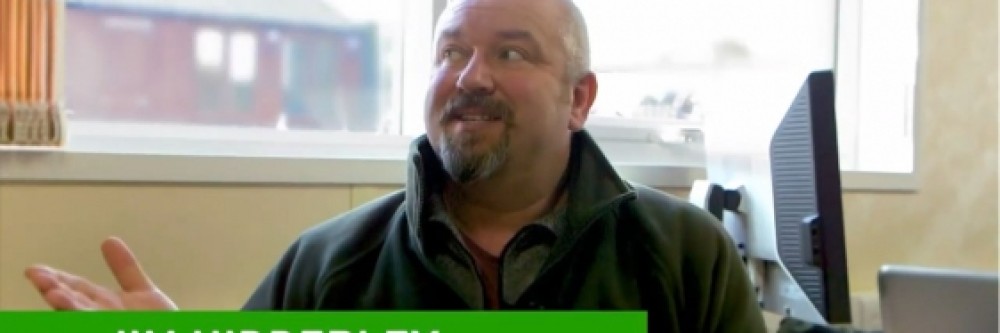
Get to Know Wernicks Refurbished Buildings Division with New Video
Wernick Refurbished Buildings (WRB) take pre-owned modular buildings and give them a new lease of life.
Buildings and materials are saved from landfill at the dedicated facility in York – and the end result is a structure that is indistinguishable from a brand new building.
In our video we get a glimpse being the curtain into the process of refurbishment.
We speak to the Depot Manager, Alan Barnes, to find out what is achievable with the method and we speak to clients who have discovered the many advantages of choosing a refurbished solution.
Hear from our clients
DB Cargo are working with WRB to replace their traditionally-built buildings and old prefab units with modular. The rail haulier explains how the process of replacing new with old has transformed their staff accommodation.
Charity Wildgoose gained a new teaching space to be proud of after working closely with the WRB team. Built on time and on budget, the 250m2 building is a space where staff and students can thrive.
Why modular?
Efficient and fast to build, modular buildings save on materials and waste during the manufacturing process.
WRB use an existing structure, which means fewer materials are required and savings are passed on to the customer.
Rebuilding an existing structure not only ensures a bespoke result but it is an environmentally sustainable alternative to traditional buildings.
Modules are transported to site and installed in 1 to 3 days – fewer vehicles and operatives on site reduce disruption to the surrounding areas and carbon emissions.
Is a refurbished building for you?
We had a lot to fit into 3 minutes – but we hope we have lifted the lid on one of the largest independent suppliers of pre-owned modular buildings in the UK.
In this era of reduce, reuse and recycle, why not opt for an eco-conscious building?
For more information, go to the website, or call our specialist team.