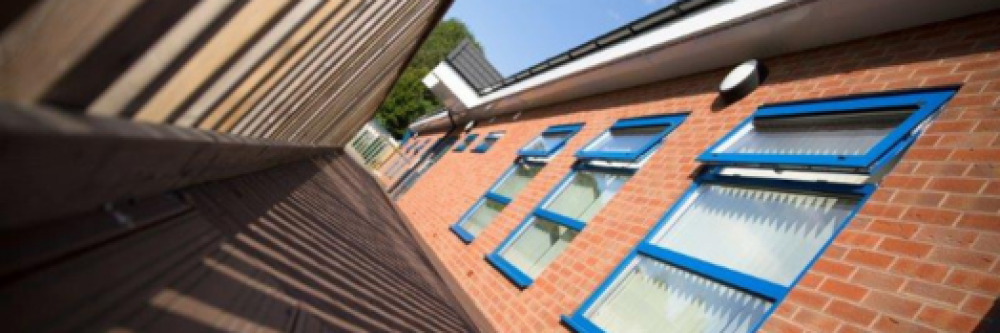
The Future is Modular: Comparing Offsite and Traditional Construction
Time, Cost, and Quality: A New Standard
One of the most significant advantages of modular construction is time. With traditional building, work is done sequentially and on-site, which means delays from weather, material shortages, or labour availability are all too common. Modular, on the other hand, is largely carried out in controlled environments, meaning the building process can happen in parallel with groundworks on site. The result is a much shorter timeline from concept to completion, with some projects completed in nearly half the time.
Cost is another area where modular often comes out ahead. The ability to lock in pricing early, avoid prolonged site-based labour costs, and reduce waste all contribute to a more predictable and often lower total spend. Traditional construction can still offer good value, especially for bespoke or architecturally complex projects, but the risk of cost overruns remains higher.
Modular buildings are also redefining expectations around quality. Modern offsite methods use precision engineering and advanced manufacturing to deliver consistent, high-quality results. With factory-based production comes tighter quality control, resulting in buildings that meet or exceed the performance of their traditionally built counterparts.
Sustainability That’s Built In
Modular construction supports the growing demand for environmentally conscious building methods. With less waste, lower emissions, and reduced disruption to the surrounding environment, it’s well aligned with government targets for carbon reduction and sustainable development. Many modular buildings are designed for energy efficiency and can easily incorporate green technologies like solar panels or heat pumps. They’re also built to adapt, making them a long-term asset that can be reused or reconfigured as needs change.
When Traditional Construction Still Makes Sense
There are still scenarios where traditional construction remains the right approach. Projects with unusual ground conditions, heritage restrictions, or highly bespoke architectural features may benefit from conventional, on-site craftsmanship. In these cases, the flexibility and artistry of traditional methods can’t be easily replicated in a factory setting.
A Growing Shift Across Sectors
Despite this, the trend is clear. More schools are turning to modular to meet urgent capacity needs without compromising on quality. Businesses are embracing modular for fast, flexible solutions that reduce downtime and disruption. With budget pressures mounting and timelines tightening, modular construction offers a way to build smarter without sacrificing standards.