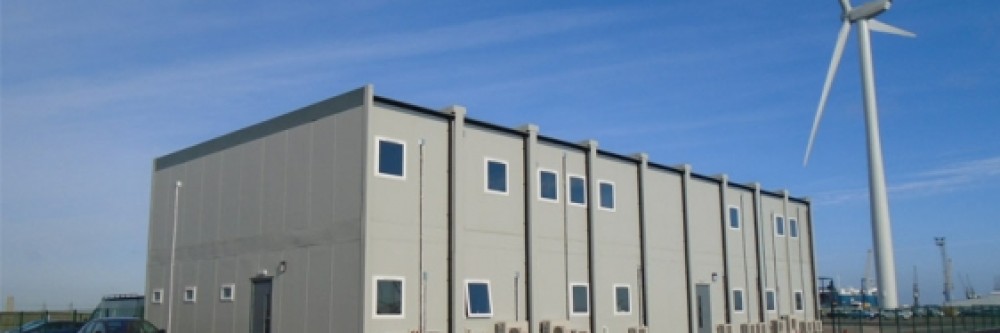
It’s Out with the Old, in with the New at Peel Ports Sheerness
The port at Sheerness is one of the core terminals of Peel Ports’ London Medway cluster, and handles a vast array of cargo including forest products, agricultural products and steel. Many of the port’s customers also belong to the automotive industry. Peel Ports has invested millions in their car importing facilities and Sheerness handled nearly half a million vehicles last year, but they aren’t stopping there. “We have a project ongoing to reorient two of our biggest automotive customers over approximately 150 acres of our dock estate,” commented Paul Miller, Project Director for the port. “This includes the relocation of one of our customer’s offices to improve the efficiency of their operation.”
The current offices are in a modular building, meaning it could have been straightforward to relocate the current building to its new location further down the dock. However, with 24 hour continuous operation required, even this solution would have meant too much disruption. A new building would be required quickly, and to deliver this Peel Ports approached Wernick Refurbished Buildings.
“Wernick were appointed through competitive tender, and they secured the contract through a rigorous assessment process of quality and cost,” commented Paul.
“This project presented us with a number of fairly unique challenges,” commented Alan Barnes, General Manager for Wernick Refurbished Buildings. “It isn’t often we’re asked to provide what is essentially a replica of an existing building.” The difference in modular systems used meant that preserving the internal layout of the original building required some very careful design solutions, especially when looking at the plumbing, but minor adjustments also allowed Wernick to introduce some improvements on the old building.
The site itself presented another challenge. While factory manufacture makes offsite programmes more resilient to weather conditions on site, there is one thing that can slow the installation process down: wind. “The site was very exposed to the elements,” commented John Reynolds, Project Manager with Wernick. “On a number of occasions high winds did mean we had to delay lifting the modules into place.” The hours lost to the wind were later recouped during the fit out phase of the project, meaning the building was delivered on time, as well as on budget.
Despite a successful install, Peel Ports still had one problem left in the form of the now vacant original building. At least, it would have been a problem if not for Wernick, who agreed to dismantle and remove it for refurbishment. “This is a great demonstration of how green modular buildings can be,” commented Alan. “We’re taking a building that may otherwise have been scrapped, and refurbishing it into a high quality product that will benefit another one of our clients. Not only is this good for the environment, but saves money for everyone involved.”
To learn more about refurbished buildings from Wernick, click here.