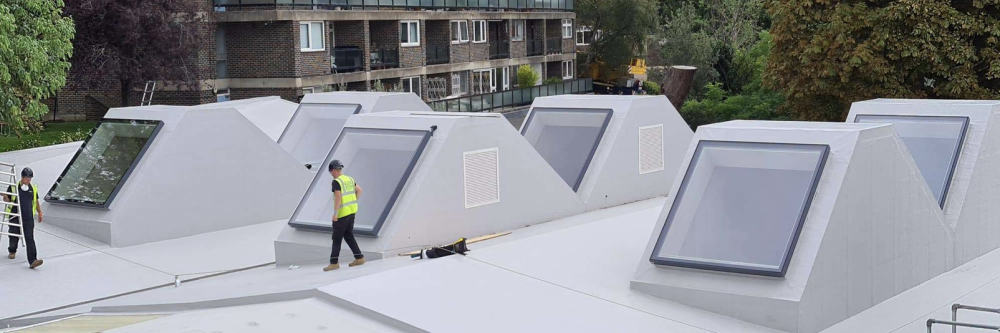
The Poppy Factory
The Poppy Factory
Polyroof’s versatile and long-lasting cold applied liquid waterproofing system, Protec, was specified for a roof refurbishment project at The Poppy Factory, due to the high level of intricacy around the roof’s design. JR Flat Roofing Ltd recognised that a versatile liquid solution was necessary in order to achieve the complex installation requirements, therefore, they looked towards Protec for its ease of application and exceptional performance benefits.
Renowned for its flexible nature, as well as being fast curing and fully reinforced, Protec extends the system’s capabilities to a wide range of roofing and waterproofing applications.
Explore the potential of Polyroof’s leading Protec System >>

Background
When it came to ensuring sufficient waterproofing of the roof at a factory-to-office conversion, JR Flat Roofing was called upon to specify and install a high-performance waterproofing solution to achieve the project requirements, enlisting the expertise of Polyroof and their liquid flat roofing technology.
The Poppy Factory has a rich and interesting history, founded in 1922 to provide employment opportunities to wounded soldiers returning from the First World War, also creating remembrance products for the Royal Family and The Royal British Legion’s annual Poppy Appeal.
Today, the Poppy Factory continues their endeavour to support veterans with health conditions, along with their families, to find employment and help them overcome any barriers. Approximately 30 disabled veterans and disabled dependents of ex-service personnel are currently employed at the Richmond-based factory, who, along with their remote contingent, hand-make 11 million remembrance poppies, 135,000 wreaths, and 1.1 million remembrance symbols every year.
The Challenge
The most significant challenge in relation to the roof was the creation of six bespoke rooflights, each ranging between 35-40m2, to improve the lux levels. The rooflights were designed on behalf of the principal contractor, Ellmer Construction, each being crafted with a timber framework spanning up to 2.7m tall at their highest point.
JR Flat Roofing subsequently coordinated the installation alongside the roofing works, as a structured phased approach was necessary to minimise disruption to operations within the office below, by ensuring the roof remained as watertight as possible.
The Solution
Once each of the timber structures were formed, they were encapsulated with Polyroof’s foil-faced SA Vapour Barrier, which subsequently provided temporary waterproofing protection. To prevent the formation of cold spots, each rooflight was then encapsulated with a warm roof design with the insulation meticulously mitred to follow the shape of the rooflight. The insulation boards were bonded with a high-performance adhesive and covered with a self-adhesive carrier membrane, again providing temporary waterproofing prior to the installation of the Polyroof liquid waterproofing system. 120mm of Polyroof Tissue-Therm Insulation was selected for the installation, with the thickness being established through thermal calculations to achieve a 0.18 W/m2K U-Value in accordance with current Part L regulations, which were applicable due to the change of building use from a factory to offices.
Due to the height of the rooflights, each were fully scaffolded to enable work to be done safely at the higher levels. This in effect created further complexities due to the multi-pitch nature of the surrounding areas, meaning the scaffolding feet had to be adjusted to account for the change in angles, whilst maintaining the provision of a solid and sound structure. The scaffolding also ensured these challenging details could be made waterproof in the safest possible fashion. An internal crash deck was provided for the rooflight works – both in the formation of the new rooflights, but also during the replacement of the large, ageing polycarbonate rooflights.
JR Flat Roofing specified Polyroof’s Protec Liquid Resin Warm Roof System as the most appropriate solution to overlay the roof. Protec is an ultra-versatile, fast curing, fully reinforced cold liquid-applied membrane that is ideal for a wide range of roofing and waterproofing applications. The system’s RapidCure technology encompasses the perfect blend of catalyst, accelerators, and inhibitors to enable full control over the cure times across a varied temperature scale, all year round. Certified by the BBA with a lifespan of at least 30 years, the seamless Protec membrane boasts combined flexibility and robustness, making it suitable for roofs of all sizes, including situations requiring regular foot traffic.
Once work began with the installation of the Polyroof waterproofing system, JR Flat Roofing approached the application by starting at the top and working down to the bottom, effectively an “upside down” method of applying the system that would usually be performed in reverse. This enabled a rapid waterproofing process and minimised any unwanted dripping, thus creating a seamless finish. A key advantage of using cold applied liquid roofing systems, is their ability to seamlessly and effectively waterproof the details.
The project was completed in two phases: the first phase with Ellmers Construction acting as a main contractor and the second phase directly for the client. The coordination with other trades during the factory-to-office conversion was crucial, and by ensuring that communication was maintained with key stakeholders throughout, the installation process ran smoothly. Throughout the project lifecycle, the Polyroof technical services team remained on hand to assist the contractors where required.
This project was one of the first to utilise Polyroof summer inhibitors, an additive that slows down the curing during hot applications, making it the ideal solution for this installation owing to the hot British summer weather during the first phase of the project. As a catalysed system, with fast curing properties, this is a further addition to enable contractors to control the cure of the liquid.
The Result
The overall project was a success, despite the level of intricacy required to insulate and waterproof the large timber rooflights. The Director of Production and Estate at the Poppy Factory, Jeff Short, was extremely satisfied with the way in which the project was surveyed, managed, and undertaken.
Here at Polyroof, we pride ourselves on the support we provide to our loyal customer base. We offer a full suite of services to ensure our clients are fully supported at every stage of the project lifecycle, including roof surveys, specification writing, thermal calculations, and more. As a UK-based manufacturer, we are supported by our top-class R&D and technical teams, who share between them many decades of knowledge and can tailor a solution to ensure your exact needs are met in the most efficient manner.
To find out more about our range of advanced flat liquid roofing systems, head over to our website today or contact us for further information.