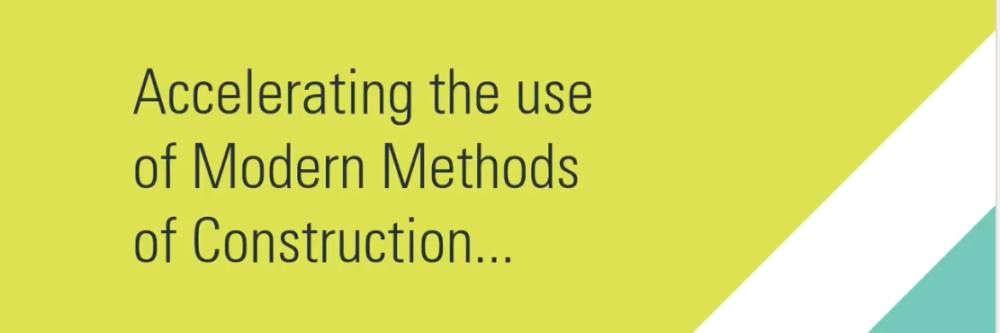
Accelerating the use of Modern Methods of Construction
In our new ‘Five minute read’ series, Balfour Beatty experts share their perspectives on important topics within the construction and infrastructure industry, discussing opportunities for the sector and sharing views on how we can increase awareness.
Modern Methods of Construction (MMC) techniques in the construction and infrastructure industry offer a major opportunity to enhance project efficiency and transform the industry.
Major projects like HS2 and Hinkley Point C are already using prefabricated modular segments, and there is a growing interest in expanding MMC practices to construct hospitals, schools, and housing. The key principle is that by adopting a manufacturing from the beginning of a project, construction teams can minimise on-site work, allowing them to focus on the intricate and unique aspects of each specific project, bringing transparency to every step in the delivery cycle, using digital tools developed internally by engineers working in close collaboration with software specialists.
The automotive industry has already made significant progress in this area by emphasising standardisation. For instance, VW, SEAT, Audi, Skoda, and Porsche share 70% of platform components, while the remaining 30% encompasses distinctive features and finishes that differentiate their products. Government-supported preliminary research showed that approximately 38% of components could be shared across various sectors such as Transport, Health, Defence, Education, and Justice, mirroring the efficiency achieved in the automotive industry.
However, the full benefits of MMC will only be realised if the entire sector embraces it, which will require cultural and structural changes across the industry.
Key factors for successful MMC adoption include:
Adopting a production mindset
Design decisions must be finalised before production begins, avoiding costly changes during construction. Components cannot be altered once they leave the factory to ensure cost, safety, and quality.
Earlier involvement of key parties
All stakeholders, including designers, manufacturers, logistics, and assemblers, should be involved early to incorporate factory-specific requirements. Careful planning from the beginning is necessary to avoid contract and supply chain pressures due to longer MMC lead times.
Demand-led change
The government, as the largest construction client, plays a crucial role in driving MMC adoption. Creating a stable pipeline of MMC projects encourages investment and attracts private investors. Publishing an MMC strategy on design standardisation is also essential.
Sector-wide culture change
Shifting from a project-based approach to a product-based approach is necessary for MMC to disrupt the construction sector positively. Product-based manufacturing supply chains require longer-term, stable demand. The Government can drive this cultural change.
New skillsets
Investment in new skillsets is crucial to harness the potential of MMC and address industry skills shortages. Skills such as manufacturing mindset, system design integration, logistics, and digital delivery strategies need to be developed industry-wide.
Building supply chain capacity
Contractors need integrated relationships with designers and manufacturing supply chains to support delivery and ensure end-to-end quality management. Investment and understanding of capacity, both nationally and internationally, are necessary to meet growing MMC demand.
MMC-supportive procurement routes
Existing procurement models should adapt to accommodate MMC cost distribution, including front-loading large orders for material manufacturing. Assessing value and allocating risk is crucial in selecting the right MMC solution.
MMC has the potential to transform the construction and infrastructure industry, align with government priorities, and improve productivity, skills, and emissions. To achieve these benefits, reducing barriers to MMC uptake, deepening supply chain collaboration, creating a demand pipeline, and improving the commercial viability of MMC adoption are essential for both the government and the sector. Balfour Beatty and MMC Balfour Beatty is at the forefront of adopting MMC approaches in project delivery.
We leverage platform solutions, invest in digital tools, and focus on staff development to instil a manufacturing mindset in our engineers. Embracing manufacturing-based construction solutions is helping us to reduce project timelines, minimise waste, and improve overall delivery, while data-driven decision making enables us to achieve game-changing efficiencies and introduce new ways of working. This streamlines processes, cuts costs, and optimises project delivery and positions us to seize opportunities as the sector transforms.
Through MMC, we are also tackling traditional industry challenges such as skills shortages, rising costs, and productivity constraints. Our portfolio includes successful showcases of off-site manufacturing in various projects, from residential buildings and student accommodation to major ventures like Hinkley Point C.
Download a copy of our Modern Methods of Construction document here.