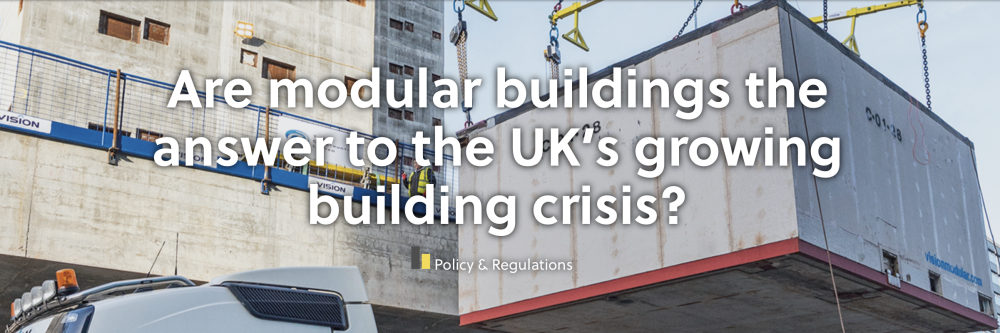
Are modular buildings the answer to the UK’s growing building crisis ? Three experts
Three experts – Steve Cole, Director of Make UK Modular; Jackie Maginnis, Chief Executive of the Modular and Portable Building Association (MPBA); and Jon Svikis, Director at Dice – discuss the possibilities of modular building.
A radical rethink is needed if Britain is ever to meet the annual 300,000 new homes target
Steve Cole, Director of Make UK Modular
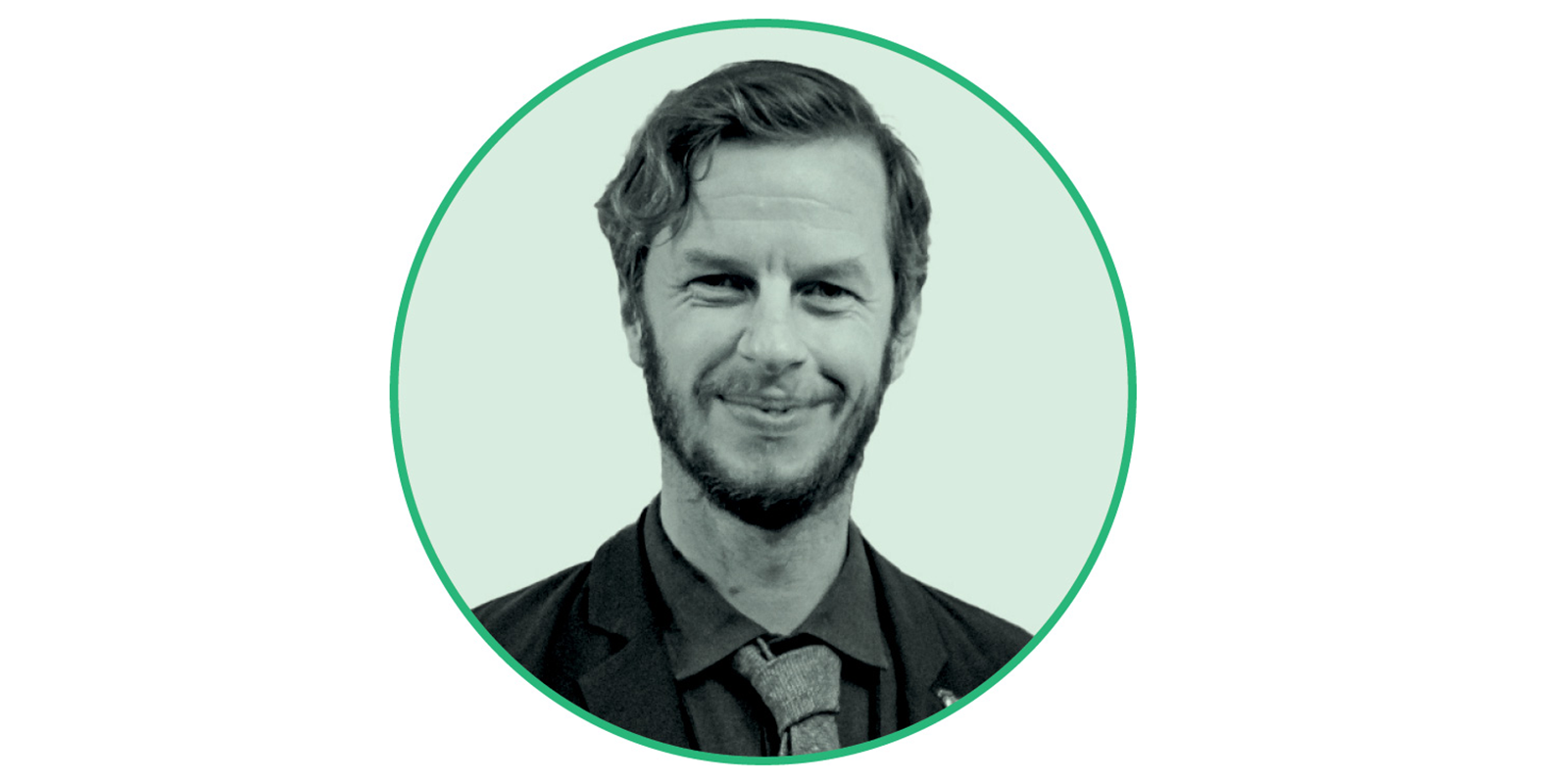
No government could come close to the 300,000 new homes a year target by 2025 without a dramatic change in the way we build houses. For a start, Britain does not have the labour force to meet the target. The traditional housebuilding sector needs to recruit 137,000 more workers just to hit the new homes target by 2030 – this means 17,000 new recruits every year, which is triple the present rate.
The current training system saw just 11,000 construction apprenticeships completed last year, and most do not enter the housebuilding industry. But that isn’t the end of the story. Some 360,000 construction workers who are due to retire by 2030 must be replaced, along with a further 24,000 to complete essential government initiatives such as remediating unsafe cladding on high-rise buildings across the country. The wider construction industry’s labour force also needs to find a way to retrofit homes to meet the government’s net-zero targets, which will require 220,000 new workers by 2030. This labour shortage equated to a loss of around £2.6bn of output in construction in 2022 and £263m of lost housebuilding output. Collectively, the whole construction industry faces the impossible goal of needing to recruit over 950,000 workers by 2030 to meet all these demands.
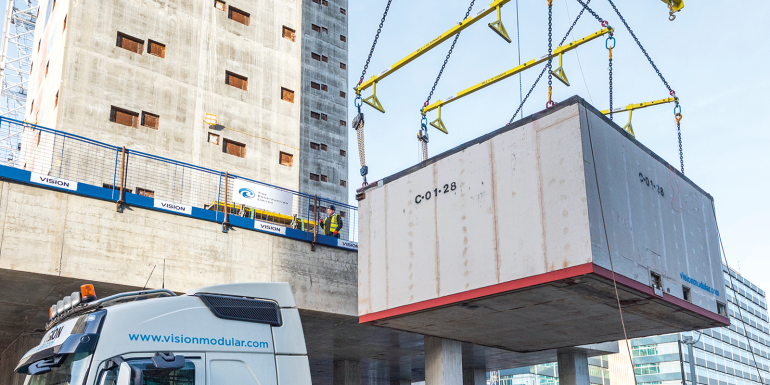
Cumbersome planning regulations and not enough money coming to the sector are often blamed for this lack of supply. Even if radical improvements to planning rules were put in place and traditional housebuilding had all the cash ministers could throw at it, the sector could not build enough homes as they don’t have the specialist workforce to make them.
Modular could be the solution, with the government’s backing to help it scale up. Modular homes can deliver factory-built houses with 50% fewer workers. That’s because factory-made houses target a different pool of workers with the skills to work in precision manufacturing. The skills needed are easy to learn on the job with in-house training, and efficient assembly line processes mean modular house builders use half the number of workers to construct the same number of homes. This builds additionality in supply. Modular is also 40% more productive than traditional housebuilding.
Modular’s in-house training model means modular manufacturers can tap into a diverse labour pool of career changers, people coming out of economic inactivity, or less qualified workers who are keen to learn new skills. Jobs are secure, full-time permanent contracts, delivering job security that does not exist within the traditional construction sector.
To address the issue of labour shortages – which is now at a critical point – the government must help modular to grow at speed and take advantage of the fact modular can build energy-efficient homes quickly. To scale up modular the government needs to:
These three changes – the levy, reallocating the money for the MMC Taskforce and dedicating a substantial chunk of the affordable homes programme to modular – would not cost any extra money. However, they would help drive faster growth in the sector and mean modular factories could operate at maximum productivity to deliver the homes Britain so desperately needs.
- remove the accidental double government levy charge on modular manufacturers by exempting them from the scope of the CITB Levy
- build supply chain capacity by repurposing the £10m allocated for the Modern Methods of Construction (MMC) Taskforce and use it to support match-funded supply chain transformation programmes based on those the government has successfully delivered in aerospace, offshore wind and nuclear; and
- solve the housing crisis faster by dedicating 40% of the affordable housing programme to modern methods of construction.
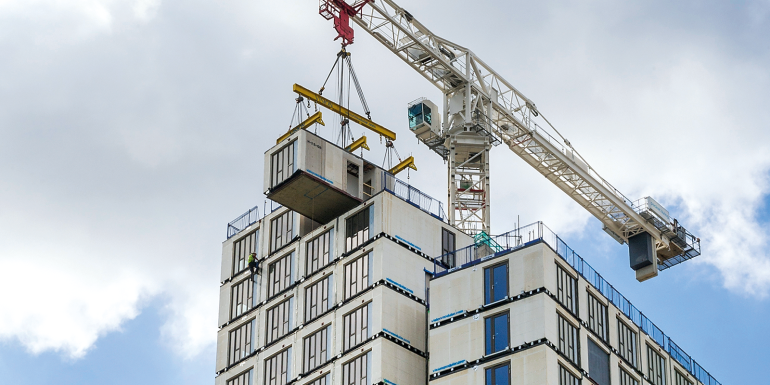
Clockwise from bottom: Apex House in Wembley; 101 George Street in Croydon; and Mapleton Cresent in Wandsworth
We need to ensure policy decisions are evidence-based to ensure the bes outcomes for building owners and occupiers
Jackie Maginnis, Chief Executive of the MPBA
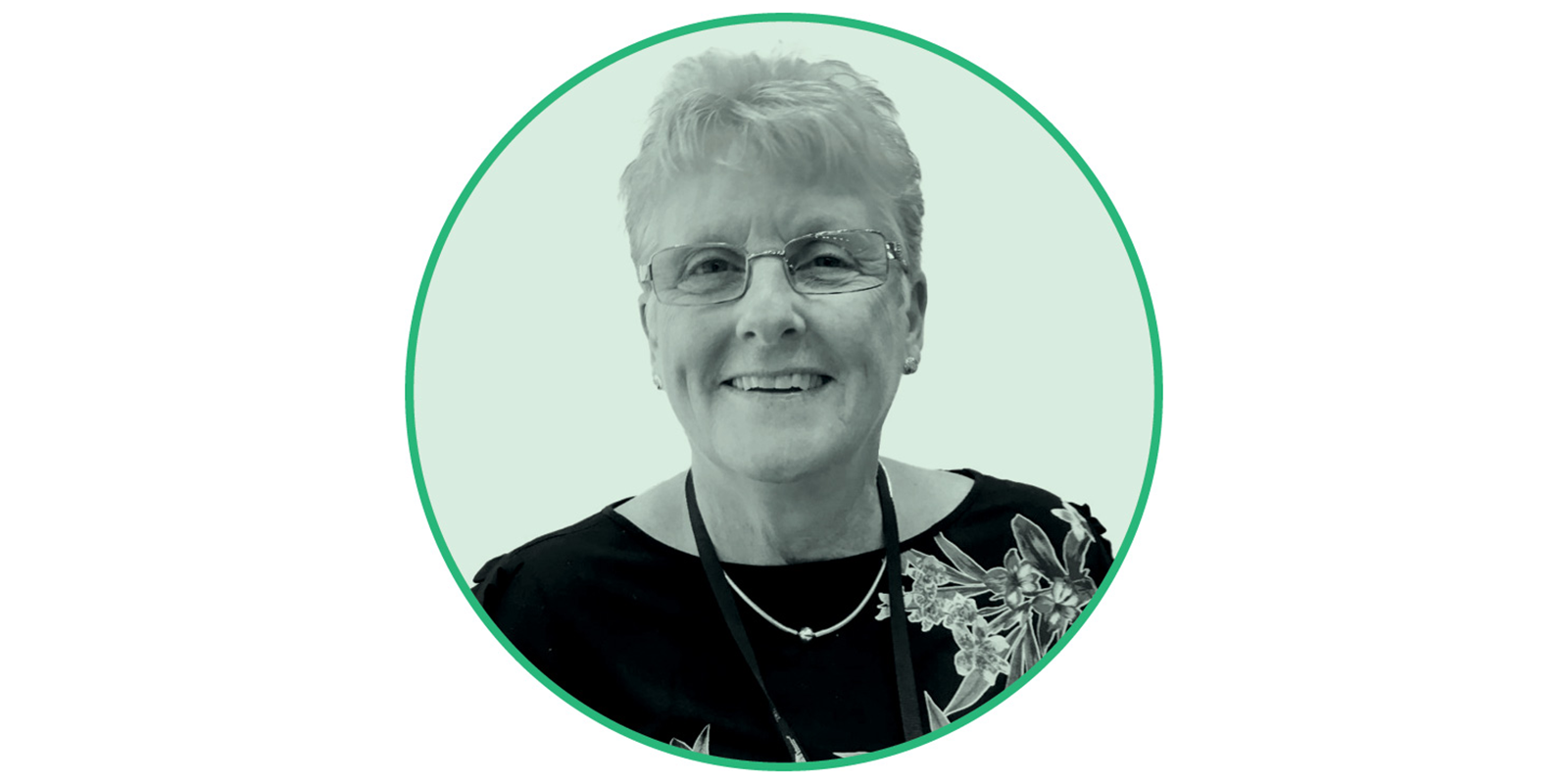
With a mission to develop a wider understanding of what can be achieved using volumetric modular construction, the public sector deserves credit. As an early adopter of MMC, councils and local authorities were using volumetric modular technology across all sectors in the 1970s and 80s, particularly to cope with a rapid increase in the need for education buildings as a result of the post-war baby boom. This was very much the development ground for MMC – backed by thinking way ahead of its time.
We cannot yet claim to be mainstream, but we have seen a dramatic uptake in volumetric modular technology, which is now considered category one in the MMC Frameworks. The support for government projects, particularly in healthcare and education, has come from lobbying over the years from the MPBA and its members to get specification and procurement changes in place. In the wake of more backing from Westminster, we have witnessed an increase in investment and modular construction frameworks across all public sector projects.
A few years ago, there was a mistaken belief that a volumetric approach stifles design capabilities. But then new architects came to the fore that not only embraced modern methods of construction but proved, without a doubt, the design potential of modular technology. Now it’s fair to say that most understand the predictability, productivity, quality and safety gains achieved in volumetric manufactured buildings.
As ever, ‘the devil is in the detail’, and there is still an element of confusion – particularly in some areas of government and wider trade bodies. This is predominately driven by a lack of understanding of the different requirements between the modular commercial and residential sectors. Policy is being dictated by the perceived growth in residential markets and then applied to the mature commercial sector – the pitfalls surrounding this approach are obvious. Then there are the global markets, particularly in the US and EU where construction methods are totally different and we cannot apply the same protocols as the UK, which is a world leader in not only volumetric modular technology but building standards.
The term ‘modern methods of construction’ was reintroduced in 2019 by Communities and Local Government following a specific commitment made in the 2017 white paper Fix our broken housing. The MMC Framework that followed as a result was specifically written for large-scale housing projects, but has been continually implemented across the wider non-domestic sectors where modular construction techniques have matured over several years. There are significant differences in the supply chain, design factors, risk profiles and – significantly – terminology used. The MPBA has released a non-domestic guide to modern methods of construction categories to raise awareness.
Modular construction quite rightly has to conform to Building Regulations. For example, combustible materials have been banned for use on the external walls of new buildings of at least 18 metres containing one or more dwellings since 2018. To our dismay, a brochure promoting a trade body in the building safety arena has an image of a timber module being craned onto about the tenth storey. It is clearly not a UK development, but this lack of attention to detail – particularly by those who are involved in setting the standards – is disappointing to say the least.
We need to ensure policy decisions are evidence-based for the good of not only the modular industry and the wider construction sector, but to ensure the best outcomes for building owners and occupiers.
This low-cost, flexible alternative to traditional building techniques could be the answe the NHS is looking for
Jon Svikis, Director at Dice Consultancy
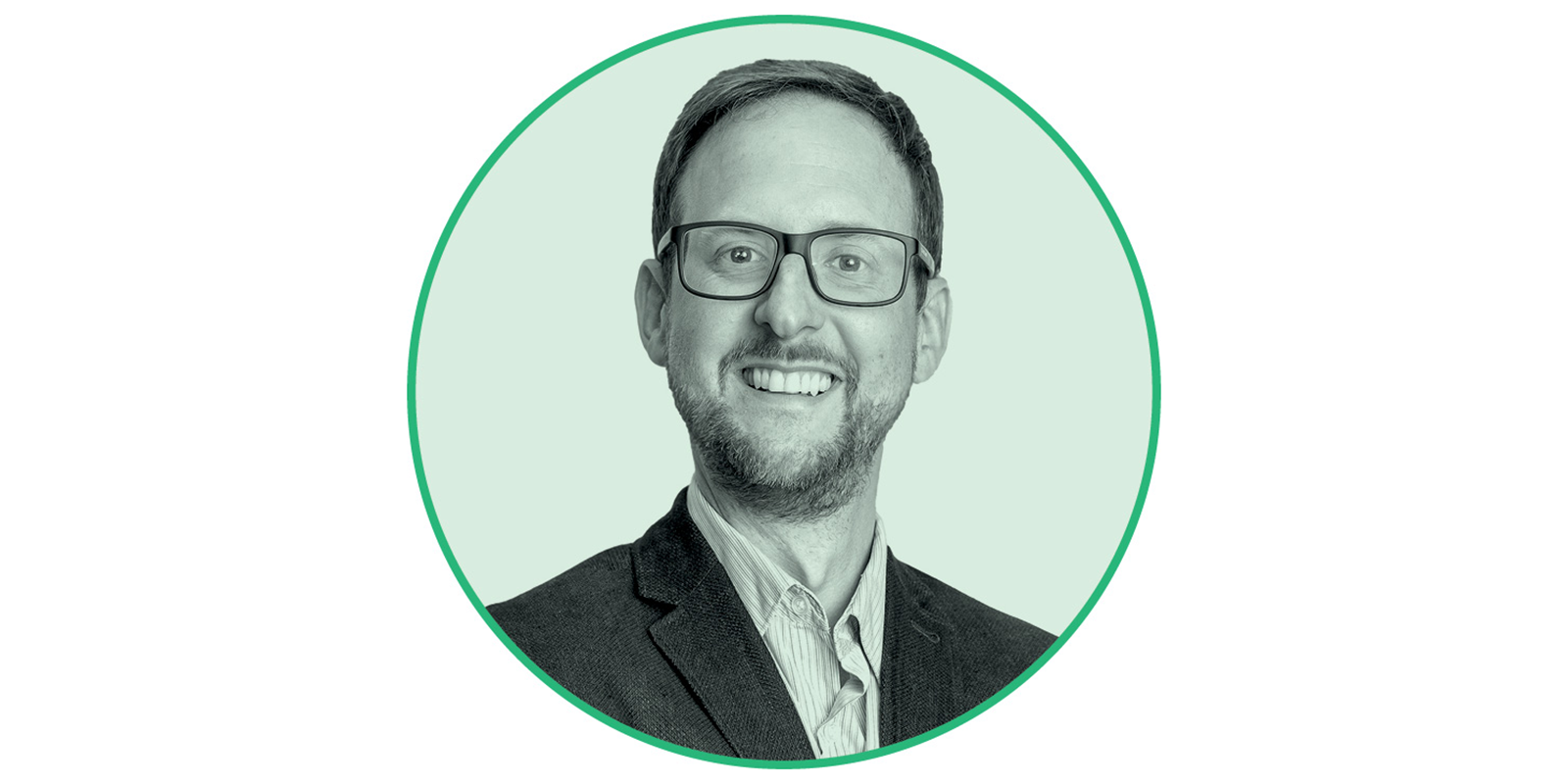
Three years ago, the government set out its ambitious hospital building programme, pledging funding for 40 hospitals using new methods of construction. Yet, with eight years left until the programme is due to be delivered, reports suggest the programme has been hit with delays and a lack of funding. The strain on the NHS and its settings around the country is well reported, and the priority now has to be implementing the building programme and ensuring new and existing healthcare facilities are fit for purpose. MMC could have a crucial role to play in improving the infrastructure of the healthcare sector.
MMC has previously been surrounded by misconception because of its lowered price tag. It isn’t lower because it’s a low-quality product; it’s lower because of the off-site manufacturing style and the fact that it requires a lot less time on-site. Construction sites can be expensive to run, so by reducing the time spent there, you can save money. MMC is also much faster. The average MMC build is 72 weeks compared to 112 weeks when using traditional methods, meaning a cost saving as well as reduced disruption.
Healthcare doesn’t stop for building work to take place – the construction has to run alongside the important work the hospital or facility is carrying out. By cutting the time on-site, the disruption to any existing infrastructure and its service is kept to a minimum, so that any new buildings don’t have a negative impact on existing ones.
This innovative way of building will also bring added flexibility into healthcare settings. Factoring in the sustainability agenda, buildings must be future-proofed against developments in the sector. For example, a number of panels and volumetric modules can be changed and re-used from one project to another, meaning materials aren’t wasted and buildings are given a new lease of life.
MMC has already been well adopted in educational and residential developments. This approach allows for buildings to be created off-site, which reduces waste, and they are designed to be more environmentally friendly and low-cost to run once they’re built. However, there is still a way to go before MMC’s potential is recognised in everything, from commercial projects to leisure and healthcare.