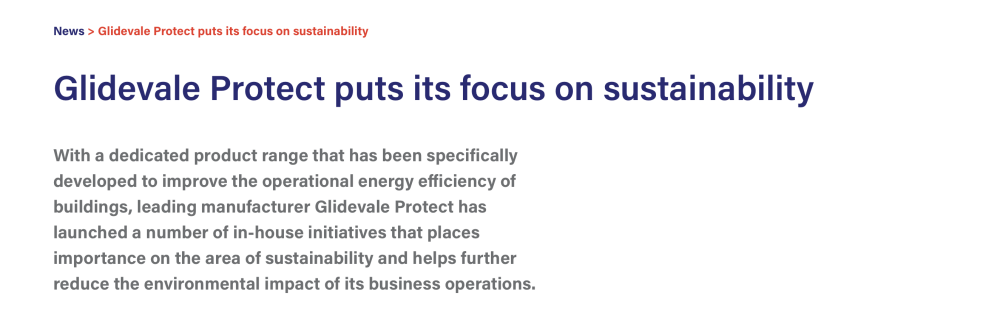
Glidevale Protect puts its focus on sustainability
With a dedicated product range that has been specifically developed to improve the operational energy efficiency of buildings, leading manufacturer Glidevale Protect has launched a number of in-house initiatives that places importance on the area of sustainability and helps further reduce the environmental impact of its business operations.
Glidevale Protect is at the forefront of designing and developing ‘hidden protectors’ such as specialist roofing and construction membranes and ventilation solutions that help build healthy solutions, improving a building’s overall thermal efficiency and airtightness, whilst reducing the risk of condensation and heat loss. The manufacturer is working on ways to improve the sustainability and operational efficiency of its business, with key projects underway including the creation of Environmental Product Declarations (EPDs) for key products, progressing towards accreditation to the ISO 50001 energy management standard and putting new systems in place to track recycling levels and energy consumption across its UK based manufacturing facilities. The business has also invested in closed loop recycling of its product waste as well as looking at how it can improve the environmental footprint of its packaging.
The company’s investment in this area has been supported by a dedicated Group Sustainability Board which meets monthly as well as the business having currently achieved its silver accreditation from the Supply Chain Sustainability School, serving to highlight its commitment to employee engagement and training.
The company’s Sustainability Board is executing a bespoke sustainability action plan and one of its initiatives is the use of an in-house conveyor to deliver closed loop recycling. This involves granulating waste ABS offcuts from its tile ventilation production line which are compounded, moulded, and recycled back into products by local suppliers based within five miles of the factory. The recyclate is then used within Glidevale Protect’s tile ventilation hoods. For rolled goods, the company is also collaborating with a recycling partner who is collecting reflective membrane waste from Glidevale Protect’s UK factories and recycling the material. A partnership is also underway with a local company who is collecting all used pallets and waste timber from the factory site for recycling.
Glidevale Protect is also working with both its suppliers and customers to reduce the plastic content in its product packaging. Currently 100% of the company’s plastic bag and shrink wrap suppliers are delivering products that contain a minimum of 30% recycled material and overall, 93% of total plastics used contain at least 30% recycled content. 95% of all cardboard boxes, roll cores and corrugated material used are FSC compliant or verified by the Forestry Commission, with suppliers confirming that all of the cardboard boxes used in the company’s packaging contain a minimum of 70% recycled material. Glidevale Protect is working alongside its suppliers to identify new ways to improve their own sustainability credentials.
Where appropriate, Glidevale Protect has already been able to remove some plastic from its product packaging for customers who have accepted reduced packaging on their deliveries. In addition, the manufacturer is also currently collaborating with selected customers on a take-back service on roll cores and stabilising cradles which are used when membranes are delivered on pallets, which will allow materials to be reused and put back into its production process.
As part of this commitment to improving its environmental impact, the company has installed EV chargers at both its UK factories and all new company cars will be either electric or hybrid vehicles.
Further updates will be announced throughout the year as Glidevale Protect identifies new opportunities to improve efficiency and reduce its carbon footprint.
Commenting, Ben Gerry, Glidevale Protect’s commercial director said: “Our commitment to supporting sustainable construction isn’t limited to our product range and as a UK manufacturer, we take our environmental responsibilities very seriously. By establishing a dedicated Group Sustainability Board and implementing a number of initiatives, with a long-term plan in place for further improvements, we are making real progress to ultimately reduce our carbon footprint. There’s still work to be done but we are committed to investing and innovating where we can to make our environmental goals a reality.”
John Mellor, sustainability lead for Glidevale Protect added “It’s important to recognise that our current activities are being implemented from the front line with both internal and external customer drivers and we are not paying lip service or greenwashing with regards to trying to reduce our environmental impact across our factory sites. Our key stakeholders within the business engage in the monthly meetings to help push through positive changes and where necessary we are consulting with industry experts who can assist us in our sustainability roadmap.”
L-R: Glidevale Protect’s commercial director Ben Gerry, senior product manager and sustainability lead John Mellor, and quality technician Dean Horner holding granulated ABS, made from waste offcuts from its tile ventilation production line. This is then compounded, moulded, and recycled back into products by local suppliers.
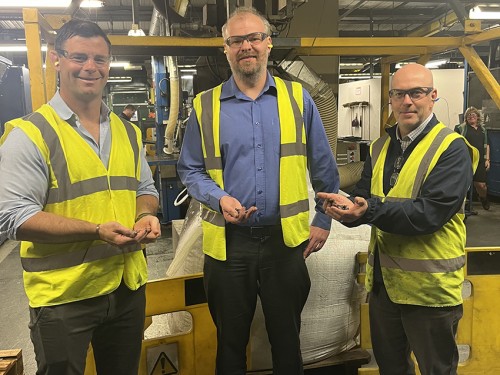
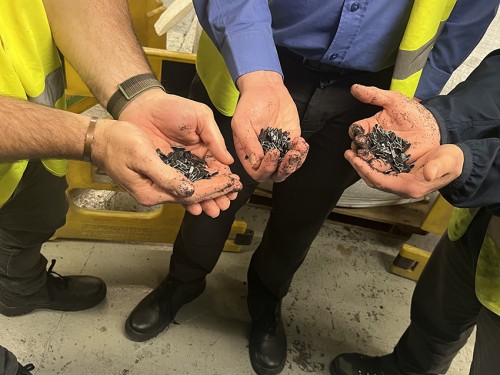