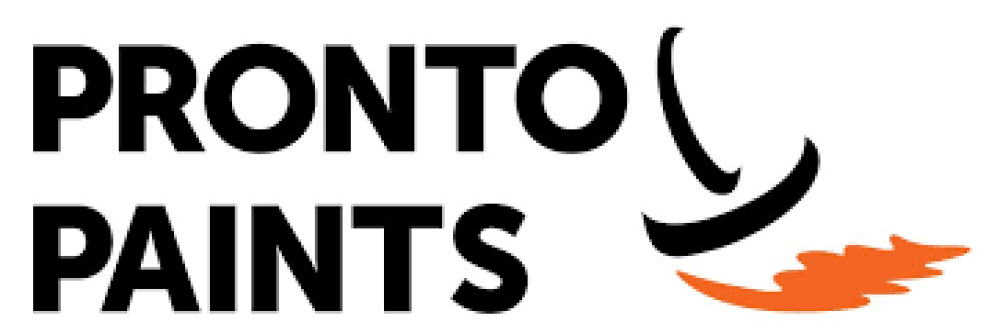
How do I select the right coating for my metal fabrication project? (Paint vs powder)
Most people when talking about metal fabrication focus on engineering and design, material selection, and the types of welding processes that are used. Metal fabrication finishes, however, can have a major impact on a finished product’s durability, functionality, and appearance.
As anodising or metal plating finishes can alter a material’s surface, painting and powder coating are applied onto a surface. These techniques offer differing levels of durability.
If you’re choosing between paint and powder coating, what are the pros and cons and which is best for a specific application?
Pros and Cons of paint vs. powder coating
Painting and powder coating can look like they have a similar appearance. Painting is typically wet application, applying an epoxy or enamel to a surface that is allowed to dry. Powder coating uses epoxies and polyester powders that are applied and melted to a surface. Powder coat curing requires high temperatures which means it isn’t suitable for many applications.
Cost of painting vs. powder coating
There is a significant up-front investment in powder coating equipment which is much higher than working with wet paint, but requires less technical knowledge for the operator. Powder coating equipment uses a stepped conveyor system and consequently the overall cost to customers can vary.
For smaller single item jobs and most industrial applications such as factory and plant equipment, skips, containers and modular buildings, painting is always going to be less expensive.
Increasingly the price of energy needs to be considered when looking at how you cure and apply any coating. We can help and advise on this aspect if required.
Thickness of coating using paint vs. powder coating
Powder coated surfaces are ultra thin, between 15-25 microns, which is important in extremely high tolerance projects. Generally, powder coating is usually a single layer and can be applied in varying thicknesses whilst wet paint can be layered to be much thicker if the need arises.
Wet paint would usually be applied at a thickness between 75-150 microns, following ISO 12944-5 alongside a blast profile could result in thicknesses over 300 microns and durability of 25 years.
For both painting and powder coating, a thicker surface means longer drying, painting schedules or curing times which adds time and cost.
Appearance of coating using paint vs. powder coating
Wet paint offers limitless choice on colours and finish options, from matte to the type of high gloss finish found on vehicles and OEM articles..
Powder coating offers more options for users seeking a textured finish. When properly applied both finishes will be even without drips or uneven sections. Powder coating can present challenges on larger components that have varying material thicknesses.
When going through the heat treatment, it has a tendency to cure faster or slower depending on metal thickness and can actually burn in some spots. In some cases, powder coating can create a checkerboard appearance or uneven shading due to inconsistent cure times.
While appearance is a key driver, any coating needs to provide protection from rust, corrosion, and external wear and tear. Preparing the surface improves the chances of a durable finish.
Pronto Paints have been working in metal fabrication for over 30 years and have an exhaustively researched range of metal fabrication coatings.
Want to book a callback or arrange a coating trial with one of our in-house experts? Drop an email to info@prontopaints.com