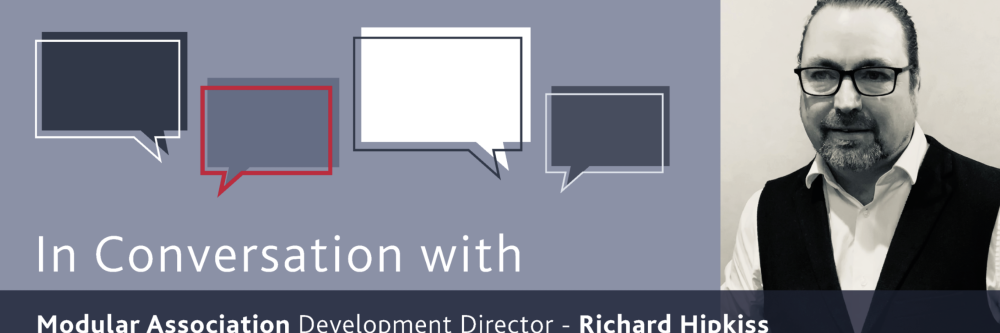
In conversation with the Modular & Portable Building Association
The Modular & Portable Building Association (MPBA) is the voice of the modular industry. Founded in 1938, its key objective is to connect all sectors of the modular and portable building industry. Today, we talk to Richard Hipkiss, MPBA’s Development Director about the modular and portable building industry and the MPBA’s role in its development and future.
1. What is MPBA’s focus and how are you supporting your members?
Since the MPBA was formed in 1938, one of our priorities has been to promote the benefits of modular and portable buildings, both in new construction and where there is a requirement for a temporary solution. Modular and portable buildings have innumerable benefits: they’re cost-competitive, time-saving, higher quality and have a lower carbon footprint.
Our work primarily focuses on changing the perceptions of the modular and portable building industry and leading its adoption of Modern Methods of Construction (MMC). In certain sectors like commercial development, modular is an established and proven method of construction, used widely. The goal is to achieve the same in other sectors, to improve the construction industry’s overall quality, cost-effectiveness, productivity and environmental impact.
To help achieve this, we offer our members specialist support and training dedicated to modular and portable buildings. We also have sub-committees championing Health and Safety, Marketing, Technical Standards and (forming soon) Sustainability.
2. Which sector – commercial, construction, health care, education or retail – currently uses volumetric modular building the most and why?
Healthcare and education are the sectors most in favour of volumetric modular builds, mainly because no other construction methodology can meet their demands in the same way. Modular is able to offer a number of frameworks that enable supply of quality buildings in a timely manner – and that’s an absolute requirement for these sectors.
Modular is also popular with the retail sector as it can go from groundworks to sales in less than two weeks!
3. What are the biggest issues and challenges the modular industry is facing at the moment?
Like the rest of the UK construction industry, the modular industry is facing two main challenges - access to materials and uncertainty over the fire regulations.
Since the tragic Grenfell Tower fire, the UK’s fire regulations for buildings have been constantly changing; it’s proven challenging for the modular industry to keep adapting at short notice.
4. Sustainability is the need of the hour. How can modular construction offer outstanding sustainability and how is the MPBA supporting its members to be more sustainable?
Modular and portable buildings are used widely in the non-domestic sectors – i.e., commercial, healthcare, education and retail – and have been found to excel in sustainability. According to a 1995 Arup report, the embodied carbon of typical modular builds was a third of that found with alternative methods using traditional materials.
To support our members to be more sustainable, we’re in the process of forming a Sustainability Committee to assist with all sustainability requirements. The committee will also be looking to renew the Arup report with fresh data.
5. Can sustainable modular construction be cheaper than conventional construction?
Modular construction has a lower carbon footprint than traditional methods of construction and is more cost-effective as factory manufacturing increases productivity while reducing costs. Not only this but, with mass adoption and more competitors, sustainable modular construction can drive extra savings.
6. What regulation changes should companies operating in non-domestic sectors – commercial, construction, health care, education, retail – be mindful of?
Recent changes to the building regulations are a challenge for all methods of construction; modular companies are no exception. Energy/sustainability and fire regulations are the big ones. Companies should be mindful of the differences across the devolved nations, too; currently there is clarity only on the regulations covering England.
7. How can companies address supply chain issues with MMC?
Good working relationships are key to resolving MMC supply chain issues. This is why one of the MPBA’s key roles is to provide a friendly, open and transparent environment – through both formal meetings and informal gatherings – where suppliers, manufacturers and installers can discuss their needs, new requirements and new technologies and work together to find the best solutions.
8. What are some tips for finding the right supplier when approaching an offsite project?
The MPBA directory is a great place to start: it enables looking into previous projects the supplier has worked on, so you can shortlist the ones you think might be right for your project. You can also ask fellow MPBA members to recommend suppliers. Once you’ve got your shortlist of potential companies, we advise setting up a meeting with each one, so you can get to understand how they work and how they can help you with your project, before you make your choice.