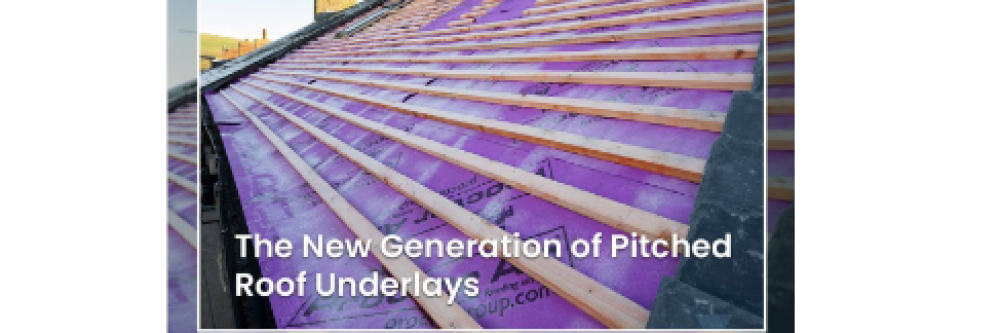
The New Generation of Pitched Roof Underlays
Hidden from view, pitched roof underlays usually warrant little attention from building users. But the latest generation of membranes can play a significant role in future-proofing buildings and protecting occupants from unhealthy indoor climates. Sue Menmuir, Technical Advisor at A. Proctor Group explains why specifiers should give new underlay solutions careful consideration.
Pitched roof underlays sit at a crucial interface between the external climate and a building’s internal climate. They are a secondary layer of weather protection below the finished roof covering, and they also influence how moisture vapour is managed within, and released from, the building.
Underlay products are usually described using the catch-all term ‘breather membranes’. This generic description doesn’t reflect the distinction between high-resistance (HR) and low-resistance (LR) membranes. Furthermore, LR membranes can be air tight or air permeable, so the generic term also doesn’t capture the role underlays can play in making sure roof spaces are properly ventilated.
Water Resistance of Pitched Roof Underlays
During installation of a roofing system, there is an inevitable period of time where the underlay will be in place without a roof covering to protect it. The underlay might therefore have to bear the brunt of any inclement weather.
The NFRC’s Technical Bulletin TB06 describes how membranes should perform in terms of water resistance. It says an underlay with “a water hold out over 1m when tested to BS EN 20811 will be adequate.”
Newly-installed roof systems can be expected to remain in place for decades. In the face of a changing climate, with an increased frequency and intensity of extreme weather, it’s essential to factor in resilience to a pitched roof specification.
Roof systems generally – and membranes as a specific part of those systems – need to be capable of withstanding more severe levels of rainfall. An underlay’s ability to perform with a 1m head of water is a minimum level of performance to look for during product selection.
Meeting the Demands of Modern Living
Water hold out on the external side must not impact on vapour permeability – or air and vapour permeability, if both are offered – from the internal side.
People generate high moisture loads within buildings, from cooking, bathing and drying clothes indoors. Now that more people have adopted hybrid working and spend more time at home, excessive levels of moisture vapour in the air are increasingly common.
As buildings have become more airtight, inadequate ventilation provision struggles to deal with these high moisture loads. Homes no longer feature open fireplaces and large chimneys, for example. Warm air rising into roof spaces therefore carries a lot of this moisture vapour with it.
As a first line of defence, top floor ceilings should be well-sealed to reduce the quantity of moisture vapour entering the roof space. However, even if a vapour control layer (VCL) is installed well initially, its continuity can be affected if modifications are made later, like adding downlighters.
Dealing with The Complexity of Roof Ventilation Specification
Roof spaces should then be ventilated to remove any moisture vapour entering the loft. Even the simplest form of roof can feature a lot of complexity when it comes to providing the correct level of ventilation.
The need for eaves ventilation alone, or a combination of eaves and ridge ventilation working together, depends on several variables.
A traditional HR membrane, like bitumen felt, doesn’t allow the passage of vapour or air. The width of the building – and therefore the distance across the roof space – then becomes a consideration. The pitch of the roof can also affect whether adequate airflow is achieved.
A more modern LR membrane might be airtight, allowing vapour diffusion but without the additional benefit of air passing through to enhance moisture removal. That prompts the question of whether the ceiling is well-sealed or not.
Whether eaves ventilation, ridge ventilation, or a combination of both is required, there is no single solution in terms of the size of ventilation openings that must be installed. And not every roof space matches the simple, unobstructed, dual-pitch roof that usually illustrates ventilation guidance.
Restrictions at eaves level (like increased insulation thicknesses), changes in roof slope (i.e., valleys and hips), and changes in construction details (e.g., a junction between a pitched roof and a flat roof) all make clear roof spaces more difficult to achieve.
Any complicated detailing – such as dormers, roof windows, compartment walls, fire barriers or changes in pitch – create separate voids in the roof slope and require more ventilation openings. They change how air flows within a roof space, reducing air flow and meaning moisture removal is not consistent across the whole roof.
Proctor Air®: An Air Permeable Lr Membrane for The Future
With all of these challenges in mind, A.Proctor Group’s new pitched roof underlay, Proctor Air, is the perfect solution for roofs of all types.
As an air permeable LR underlay, no VCL is required in the ceiling and no additional ventilation measures are required in the cold roof space. The membrane permits the passage of both air and moisture vapour through the roof construction, to the outside.
Proctor Air reduces the risk of issues occurring in roof spaces due to poorly installed VCLs or ventilation, since neither is needed. In fact, Proctor Air provides a more uniform flow of air than normal vents, helping to prevent ‘dead’ areas of poor ventilation in complex roofs.
Among other benefits, Proctor Air’s water resistance has also been tested and meets the threshold of over 1m of water holdout recommended in the NFRC’s Technical Bulletin TB06.
Where periods of severe inclement weather, or prolonged exposure, are expected during installation, BS 5534 and BBA Bulletin 2 advise that temporary protection be considered. This is especially important in retrofit projects, where occupants are likely to remain in residence or there are sensitive internal finishes.
A. Proctor Group is a 4th generation family business with a history of technical innovation, promoting good practice, and developing products that roofing contractors want to use. We have applied this wealth of experience to creating the next generation of air permeable LR membrane.
By choosing and installing Proctor Air, specifiers, contractors and building owners/managers can enjoy the confidence that comes from a high-performance product doing its job without intervention. All of this is backed by our unique 15-year warranty, offering peace of mind even in the face of an uncertain future climate.
For more information visit: https://proctorgroup.com/products/proctor-air