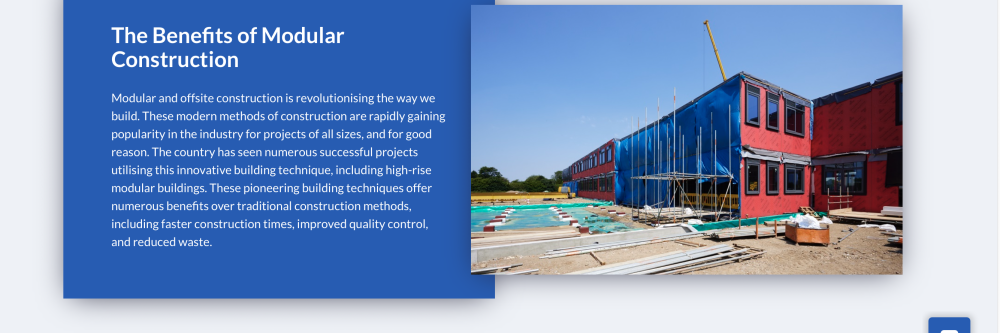
The Benefits of Modular Construction
Modular and offsite construction is revolutionising the way we build. These modern methods of construction are rapidly gaining popularity in the industry for projects of all sizes, and for good reason. The country has seen numerous successful projects utilising this innovative building technique, including high-rise modular buildings. These pioneering building techniques offer numerous benefits over traditional construction methods, including faster construction times, improved quality control, and reduced waste.
One of the key advantages of modular and offsite construction is speed. This is particularly important in the UK, where construction timescales are often critical due to weather conditions and other factors. Modular construction allows for much of the construction work to be done off-site, which greatly reduces the time needed on-site. This can lead to faster project completion times and reduced disruption to the surrounding area.
One notable success in the UK has been the use of modular construction to deliver high-rise buildings. Wembley, London is home to the impressive Apex House project. This 29-story tower was built using modular construction and was completed in just 12 months. The building includes 560 student apartments and is one of the tallest modular buildings in the world. Another notable modular construction project in the UK is the Mount Pleasant project in London. This development includes 136 affordable homes that were built using modular construction. The homes were also completed in just 12 months, which is significantly faster than traditional building methods. The modular construction process also allowed for a high level of customisation, with each module being tailored to the specific needs of the development.
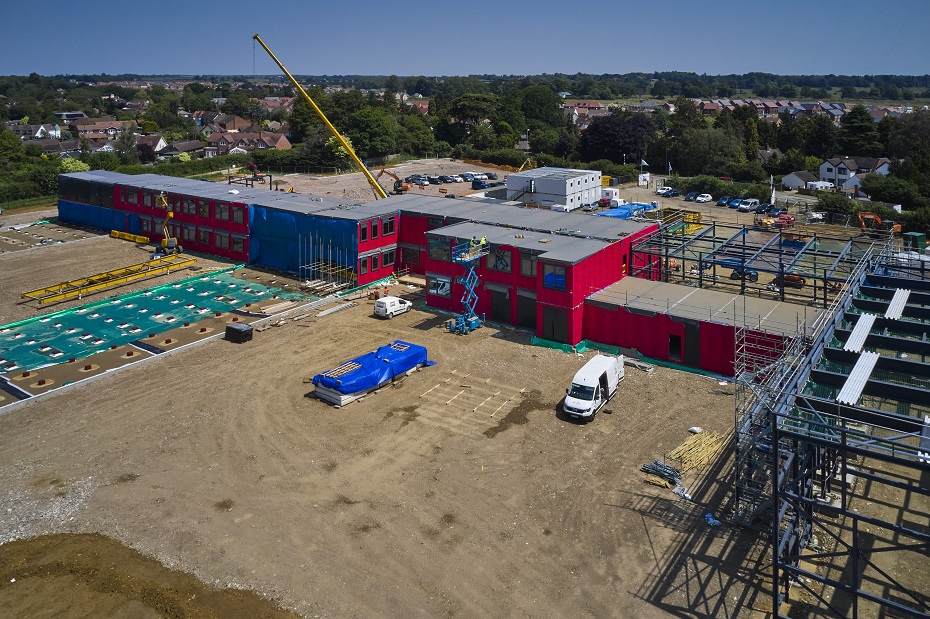
Algeco UK Ltd has secured a Department for Education (DfE) funded project for the offsite construction of Northampton School for Boys Multi-Academy Trust. The project was secured via the MMC1 Lot 1 modular framework (*DfE published contract value is £27.6m). Algeco, acting as Principal Design & Build Contractor and working with Watson Batty Architects, is providing a full turnkey solution. A total of 210 modules will be supplied by Algeco using the innovative Seismic technology, plus a hybrid structure for the halls, to create the 1200 place new secondary school, including sixth form provision. The first modules, which will be manufactured by Algeco in its Carnaby facility in East Yorkshire. Handover of the completed school is scheduled to take place in 2024. Utilising Seismic technology for the Northampton school modules will deliver important benefits; it is 75% faster and achieves a 47% improvement in value compared to traditional construction techniques; it even offers a 33% improvement in speed when compared with standard modular construction. In terms of sustainability, Seismic delivers significant reductions in both operational and embodied carbon of up to 70%. This is achieved through factors including design efficiency, materials selection and manufacturing effectiveness, leading to limited wastage.
There are many benefits to modular and offsite construction, including improved quality control, reduced waste and the potential to be more sustainable than traditional construction methods. Improved quality control is due to the modules being constructed in a controlled environment, where the quality of the materials and workmanship can be closely monitored and controlled. This can help reduce the risk of errors or defects in the final product, leading to a higher quality finished building. This optimised construction method also assists waste reduction with the efficient use of materials. Modular construction is considered more sustainable for several other reasons. One of those reasons is because modular can reduce the carbon footprint of a building project during the construction period. Manufacturing, transportation and the use of large machines and equipment on traditional construction sites all contribute to carbon emissions, something which modular and offsite manufacturing greatly reduces by the very nature of the process taking place in a factory environment. Less disruption to the surrounding area of the construction site itself can help preserve natural habitats and reduce the impact of development on the local ecosystem.
At the A. Proctor Group Ltd. we are proud to be a part of the modular construction revolution. Our range of building solutions, including insulation and membranes, are designed to support the unique needs of modular construction projects. We are committed to providing our clients with the highest level of technical support and expertise to help them achieve their goals. If you’re interested in learning more about modular construction and how our products can support your project, please do not hesitate to get in touch.
In conclusion, the UK has seen numerous successes with modular construction in recent years which have been noticed all over the world. The speed, efficiency, and customisation offered by this building technique have made it an attractive option for a wide range of complex projects, including high-rise buildings. As the construction industry continues to evolve, it is likely that modular construction will continue to play an important role in shaping the future of building in the UK.
Adam Salt – Business Development Manager at the A. Proctor Group
Photo Credit: Wraptite used in Northampton School for Boys Multi-Academy Trust.