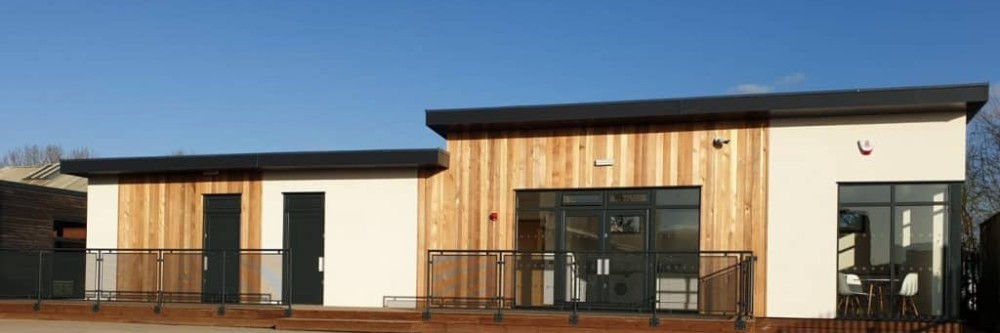
What is net zero construction?
Net-Zero in use or in construction?
The term net zero has become familiar to many people but it can in fact mean two different things for a building, either that it is net zero carbon in operation or that it is net zero carbon in construction.
In this guide, we’ll explain the difference between the two and outline the steps that TG Escapes and other companies in the industry are taking to meet net zero construction goals when building in education, for homeowners, in commercial and leisure settings, or for office buildings.
In 2008, the UK became the first major economy in the world to pass into law international commitments to end its contribution to global warming by 2050. The Climate Change Act of 2008, amended in 2019 to comply with the 2016 Paris Agreement for Climate Change, commits the UK to bring all greenhouse gas emissions to net zero.
Any emissions that cannot be prevented by this time must be balanced by schemes to offset an equivalent amount of greenhouse gases, such as planting trees or using technology like carbon capture and storage.
During this period, the signs of climate change have become increasingly widespread and the term net zero carbon has entered mainstream awareness and language. However, net zero construction has yet to be categorically defined and means different things to different corporate organisations, companies, governmental bodies, civil groups and individuals.
Why is net zero carbon construction such a priority for the UK building industry?
Globally, the built environment sector is currently responsible for almost half of greenhouse gas emissions, so if the Government’s commitment is to be achieved then the British construction industry needs to urgently address the issues of energy-efficient building design and net zero carbon construction process within a net zero context.
However, the concept of a net zero carbon building is subject to differing interpretations and meanings. Some focus purely on the energy consumption during a building’s day-to-day use, some on the creation of the structure and others still on the entire life span of a building from the laying of the first foundation through to its demolition and removal.
The UK Green Building Council (UKGBC) has been playing a vital role in developing a workable definition to assist the construction industry in its development of buildings that achieve the net zero carbon objective. In its document “Net Zero Carbon Buildings: A Framework Definition” they have adopted a two-pronged approach to defining a net zero building, comprising operational use and construction practice, the latter often accounting for half or more of a building’s carbon emissions.
How is net zero construction defined?
The starting point for a definition of net zero construction is:
“When the amount of carbon emissions associated with a building’s product and construction stages up to practical completion is zero or negative, through the use of offsets or the net export of onsite renewable energy.”
Likewise, the current definition for a building that is net zero in use is:
“When the amount of carbon emissions associated with the building’s operational energy on an annual basis is zero or negative.”
Operational energy includes heating and cooling systems, cooking, lighting and plug loads. Construction energy should incorporate the potential costs of adaptability and flexibility, alongside the impact of deconstruction. This considers the total carbon emissions created through construction, adaption and deconstruction over the building’s lifetime.
Only when both elements satisfy a net zero ideal can a building be deemed to fully comply with the aims of the Climate Change Act and fit within the Government set targets of 2030 for operational net zero and the 2050 embodied target.
The UK laws behind net zero
The disciplines and practical methods necessary to achieve true net zero construction are in the early stages of development. However, we expect to see the rapid, iterative evolution of the principles and metrics which will become subject to sharper definition, allowing for a tighter set of guidelines.
The resulting system of recommended building methods, practices and policies will be created in a spirit of collaboration and consensus amongst the construction industry community including builders, designers and policymakers. The government has initiated this with specifications PAS 2050 for assessing the lifecycle greenhouse gas emissions and PAS 2060 to demonstrate carbon neutrality for certification.
Until such time as a legally binding set of net zero building regulations is created, the general principles that the UKGBC is encouraging the construction industry to adopt are threefold.
Firstly, the polluter pays and any emissions made should, ideally, be measured and offset as they occur. Secondly, the measurement of emissions should be accurate (not estimated) and the data collected must be made available transparently and publicly. Finally, action should take place now, before the formulation of prescriptive requirements.
SBEM and Passivhaus
The Simplified Building Energy Model (SBEM) is the Government approved software tool used by architects and designers to calculate anticipated CO2 emissions of a building at the design stage, aiding net zero construction goals.
Studies have shown that there can be a performance gap between SBEM-calculated emissions and in-use monitored values. This was first identified by Weber in 1997 when the gap was calculated at 30%, and more studies have shown this can be significantly higher.
There are various opinions about where the performance gap comes from such as inadequate construction and maintenance or a deviation in use from the original design criteria. However, the SBEM calculations can be enhanced by looking at tried and tested commercial modelling systems such as the Passivhaus Planning Package which, when reviewed against monitored performance, was found to range within 5-10% of the calculated result with elements of overachieving.
What is the future of net zero construction?
At present, the UKGBC stipulates that the primary priority in achieving net zero operational energy efficiency is to reduce both the demand for and consumption of energy, while ensuring that all energy used should be calculable and disclosed. With regards to net zero carbon construction, a whole-life carbon assessment should be undertaken (and disclosed) and all embodied carbon impacts from the products and construction methods used must be measured and offset.
In both the use and construction of a net zero building, every effort must be made to utilise renewable energy supplies (both on and off-site) and any remaining carbon should be offset using a recognised framework, again to be publicly disclosed.
In August 2020, The Government Property Agency issued a paper entitled “Net Zero and Sustainability: Design Guide.” Although the document is aimed specifically at the Government’s own building estate, it has drawn heavily on the UKGBC framework to identify the steps and processes that a project team should undertake to deliver a net zero building. Until similar papers are published for the private construction sector, it is probably a good indicator of what should be expected.
Clearly, there is a lot of detail that is probably best left to the experts, but the following points cover most of the core elements of the recommendations made:
Net-Zero Carbon Construction:
- Natural, sustainable materials should be considered first, avoiding high embodied carbon materials wherever possible and still ensuring longevity.
- Efforts should be made to use fewer materials generally and to reduce the weight of dead loads, thus minimising structural weight and reducing foundation load and size.
- Transportation to the building site and onsite construction should be reduced by utilising offsite construction.
- Waste and site works should be minimised and the construction materials and methods used should allow for future demounting, replacement or reuse of the structure or its elements.
Operational Energy:
- Glazing should have high U values and, where possible, have a low surface area, whilst balancing the need for natural daylight and thermal comfort. All windows should be openable to allow cross ventilation.
- All systems for heating, cooling, pumping and fans should include demand controls.
- Fossil-fuelled heating and hot water systems must be avoided and renewable energy sources should be maximised. The installation of onsite renewable energy sources, and battery storage, should be considered
Bespoke net zero modular buildings designed and built
TG Escapes follow a strict construction ethic of sustainability and energy efficiency and are keen to remain at the forefront of the quest to create net zero carbon buildings that are both affordable and able to enhance the well-being of their occupants. In order to reduce carbon emissions worldwide, it’s necessary for industries like ours to adapt.
We already design buildings that are net zero in operation with the use of appropriate renewable energy technology. You can read a detailed case study about our net zero building at Samuel Ryder Academy. We also construct buildings that fulfil the vast majority of the recommendations made to achieve buildings that are net zero in construction.
On our journey to becoming a net zero business, we can offer whole-life carbon-neutral buildings, comprising low-carbon materials and 100% onsite renewable energy. We are working with the Carbon Trust to build a tool to independently measure this in a way that it can be certified to the international carbon-neutral standard PAS2060.